近年来,“新技术、智能制造、自动化生产”成为家具行业内的热点话题。随着全屋定制行业的发展逐渐加快,工厂对家具零部件的生产要求也是一日比一日提高。零部件生产的标准化,模块化,智能化已经成为重点的发展方向,而其中钻孔就是板式家具生产过程中的一道核心工艺,钻孔的质量和效率将直接影响到整体生产的有效运作。
在实际生产中,只有明确哪些因素影响了钻孔质量和效率,才能够做到“对症下药”,从而提升钻孔能效。笔者经过调研分析,在分析当下主流钻孔设备的基础上,总结了一些影响家具钻孔的因素,以供行业参考。
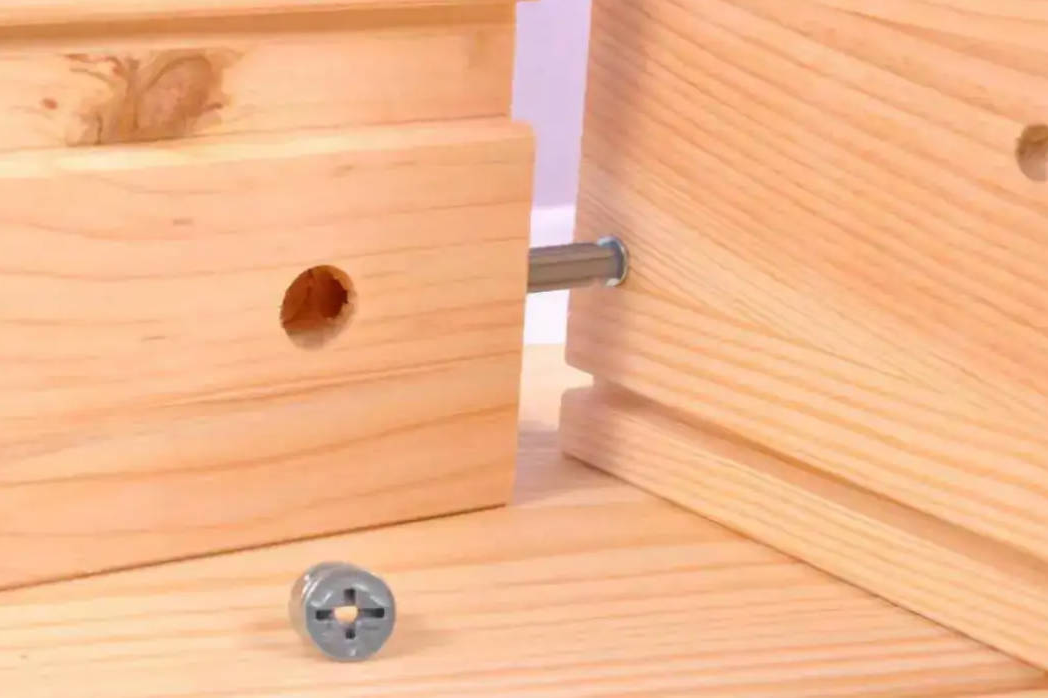
01 钻孔工艺可谓“难而重要”
钻孔是实现家具板件与板件之间相互连接的接口,尤其在板式家具中,其零部件钻孔的类型主要有:用于圆榫安装和定位的圆榫孔;用于螺栓,螺钉定位以及拧入的螺栓孔;用于各类铰链安装的铰链孔;用于各类连接件,插销安装和连接的连接件孔等等。
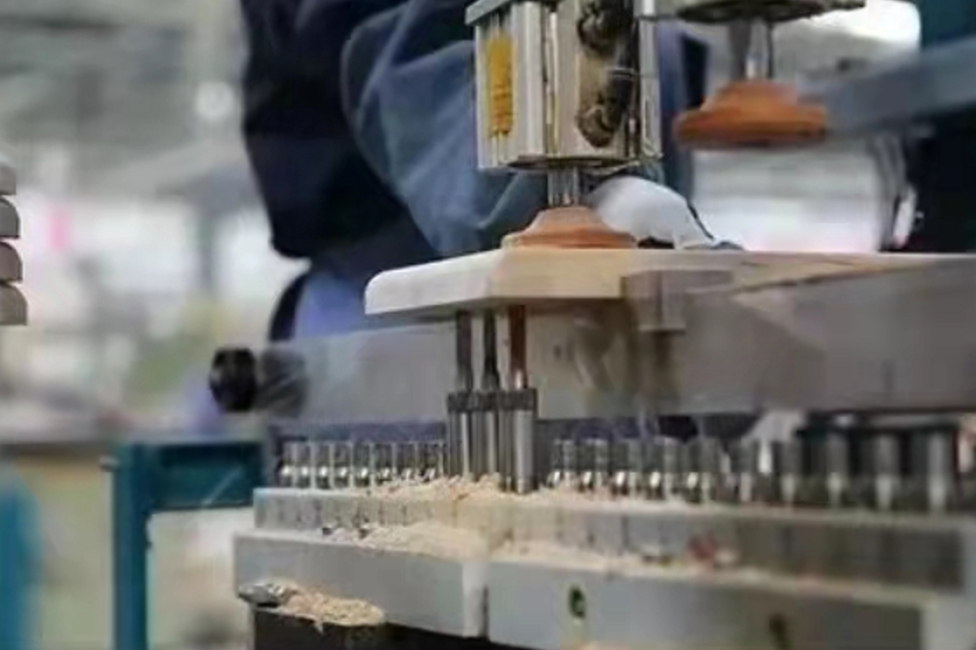
放在整个家具制造工艺中,钻孔工艺其实颇具难度,因为钻孔的技术要求很高,成本投入也大;与此相匹配的,钻孔设备的性能好坏决定了钻孔的质量,只有精准的钻孔才能生产出高品质、稳定的家具产品,因此钻孔很大程度上决定了家具的品质。
02 钻孔设备是“生产之利器”
对于板式定制家具企业而言,面临大规模定制的生产现状,钻孔工序往往是企业的瓶颈工序。传统的钻孔设备如单排钻、多排钻已不能满足日益多元化的需要,数控化、柔性化的高端数控钻应运而生并不断发展。目前大多数家具生产企业,往往都会配置排钻与数控钻,以适应不同的生产需要。
02-1 排钻设备
在家具生产中,排钻是钻孔的专业设备。排钻可以分为单排钻和多排钻。单排钻的排座只有一排,自动化程度相对来说比较低,相应的精度要求也会低。因此,在现代化的家具工厂中几乎看不到单排钻。
目前为了提高家具的生产效率,企业大多采用多轴排钻来保证钻孔的精度。多排钻有3排,6排,8排等等。在大规模的板式家具生产中,6排钻是比较常用的典型的生产设备。6排钻的最大优势在于可以在定位一次基准后,就可以完成相应的板式家具零部件的打孔要求,具有加工效率高,精度高等优点。
过去家具生产,排孔为技术难点,对操作人员要求高,需懂工艺、设备操作等各方面要求。现在的数控排钻可实现数据的对接,可通过扫码直接调取钻孔程序实现钻排、定位靠档等的自动调整,减少对人员的操作要求。
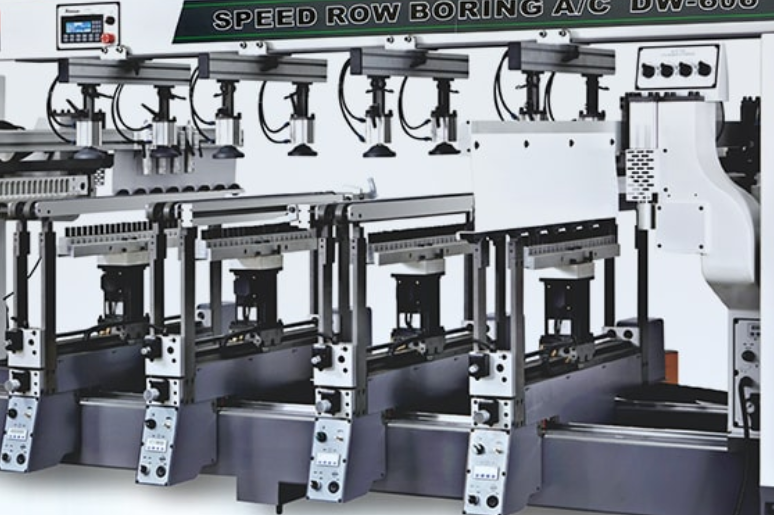
02-2 CNC钻孔中心
CNC钻孔中心就是计算机控制下的数控钻。对于工件结构复杂,内封闭或外封闭曲线形状的板件,其孔位分布较零乱,宜采用 CNC 打孔中心。而周期性、小批量轮番生产,市场需求变化快,价格高,受流行趋势变化影响的工件加工,也适宜采用CNC打孔中心。
家具生产企业常用的数控钻孔有工位式CNC钻孔,往往具有钻垂直孔、水平孔、拉槽、铣型的功能,而且具备双工位,可交替进行作业,适合于定制家具各种尺寸板件的加工;
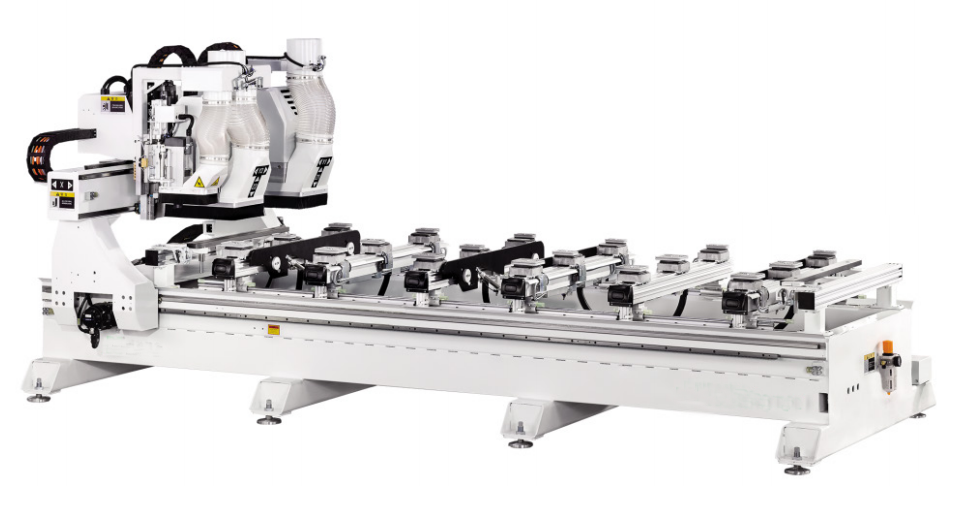
通过式CNC钻孔,具有高柔性、高智能、高效率的特点,集自动进料、加工、出料为一体,而且操作简单,钻孔加工速度快,适用于加工各式组合柜体板式家具;
六面数控钻,通常可以一次性完成六个面的钻孔及两个垂直面的拉槽,对操作工人要求简单,是其一大特点,俗称“傻瓜式”操作,拆单数据导入后人工扫码即可加工,可单台使用,也可多台并联使用,能够有效节省人工。
在CNC 钻孔方案中,六面数控钻的钻孔方式更为柔性,由于定制家具制造在不断引进新五金件及新工艺,对CNC 的智能化多工艺生产需求日益增加,部分企业数控六面钻已实现了多功能钻及铣的功能,进一步加快了定制家具的生产效率及加工精度。
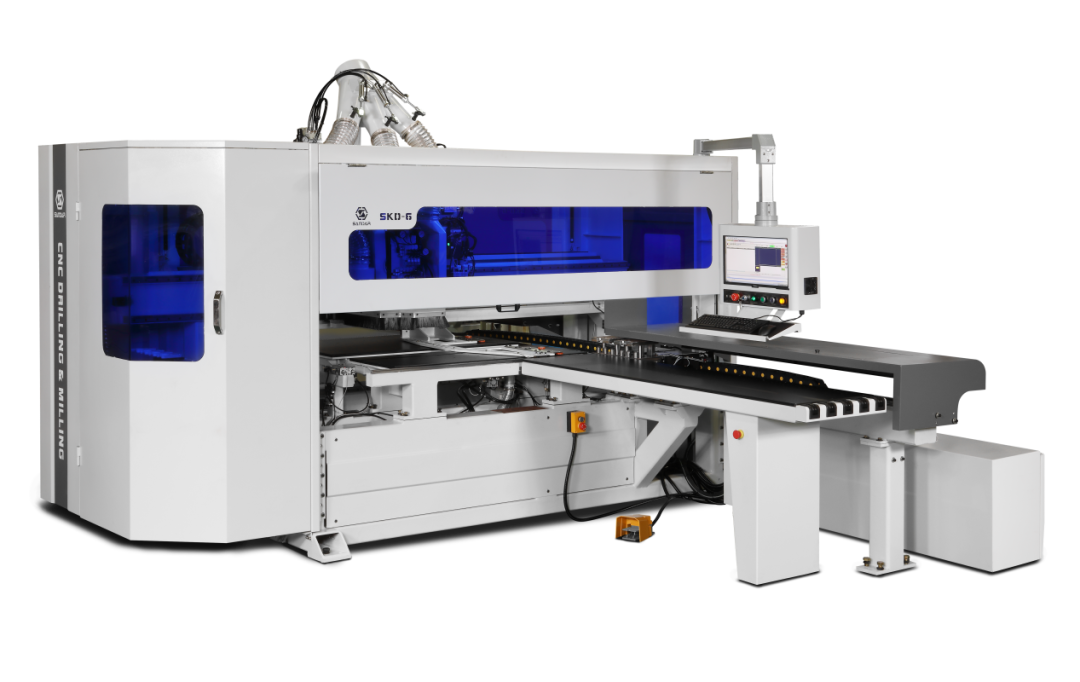
03 什么在影响钻孔质量和效率
03-1 孔位的设计
“32mm系统"是在反复的生产实践中诞生,并且作为世界板式家具的通用系统。因此,在板式零部件的孔位设计上要遵循32毫米的孔位设计,保证孔位的中心距离是32毫米的整数倍,在生产的过程中可以实现模块化的一次性打孔,保证标准化的孔位,孔距和孔径。
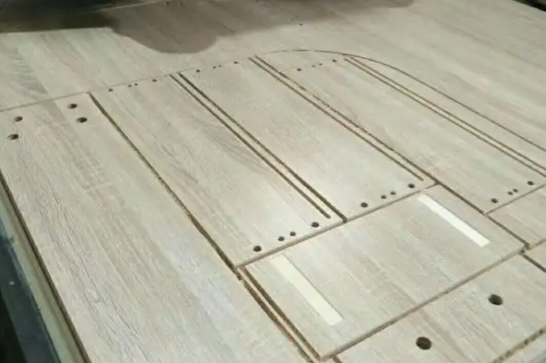
一般情况下,32毫米系统是以旁板为核心,柜类家具的零部件都要与旁板发生关系。如果旁板的孔位置确定以后,其他零件的相对孔位置也可以得到确定。如果相邻两侧板的孔距不是32毫米或者其倍数,那么就需要对孔位的间距进行调整,从而导致不能够一次性的打孔,影响打孔的效率以及打孔的精度。
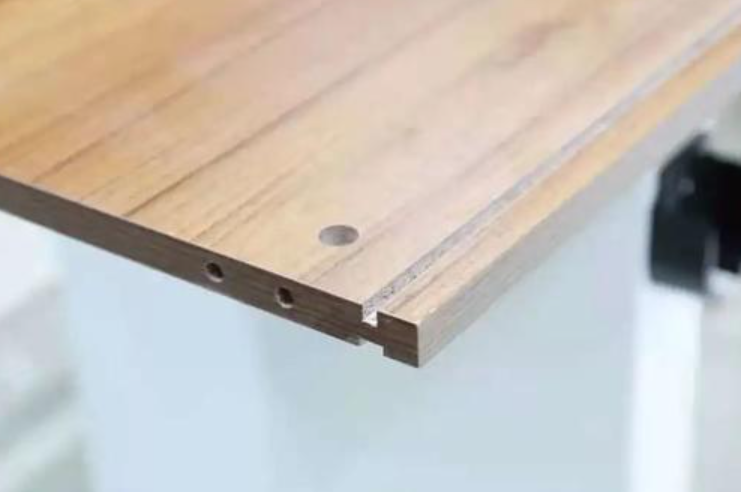
03-2 工人的熟练度
笔者在走访工厂的过程中,了解到目前很多传统家具企业的生产线的流水工人大多缺乏严格以及系统规模化的技能培训。比如说:读图能力,数据的录入,机器的调试等等问题。在传统的排钻工序中,几乎所有的操作流程都会涉及到人的主观性,即使是使用数控排钻,也同意涉及人工协作。
由此,我们可以总结得出:如果钻孔作业中人为因素的占比高,那必然会加大失误的概率,在某种程度上,板件的钻孔质量会有一定程度的降低,同时也是效率低下的体现。
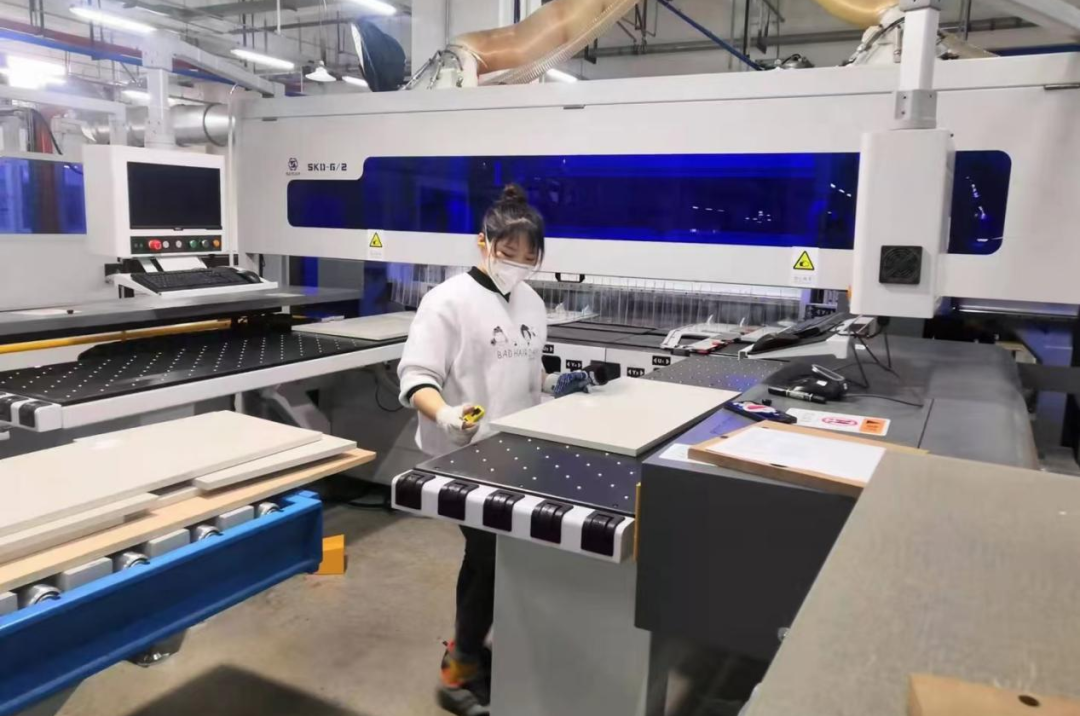
03-3 有效加工时间
钻孔的加工质效,取决于有效加工时间,包括标准工时与辅助工时,它们是影响家具钻孔质量和效率关键因素。标准工时是指的是家具零部件所需要的钻孔加工时间,辅助工时指的是在钻孔相关的生产管理服务中所需要花费的时间。如果想要提高钻孔的效率,降低标准工时、减少辅助工时是有效途径。
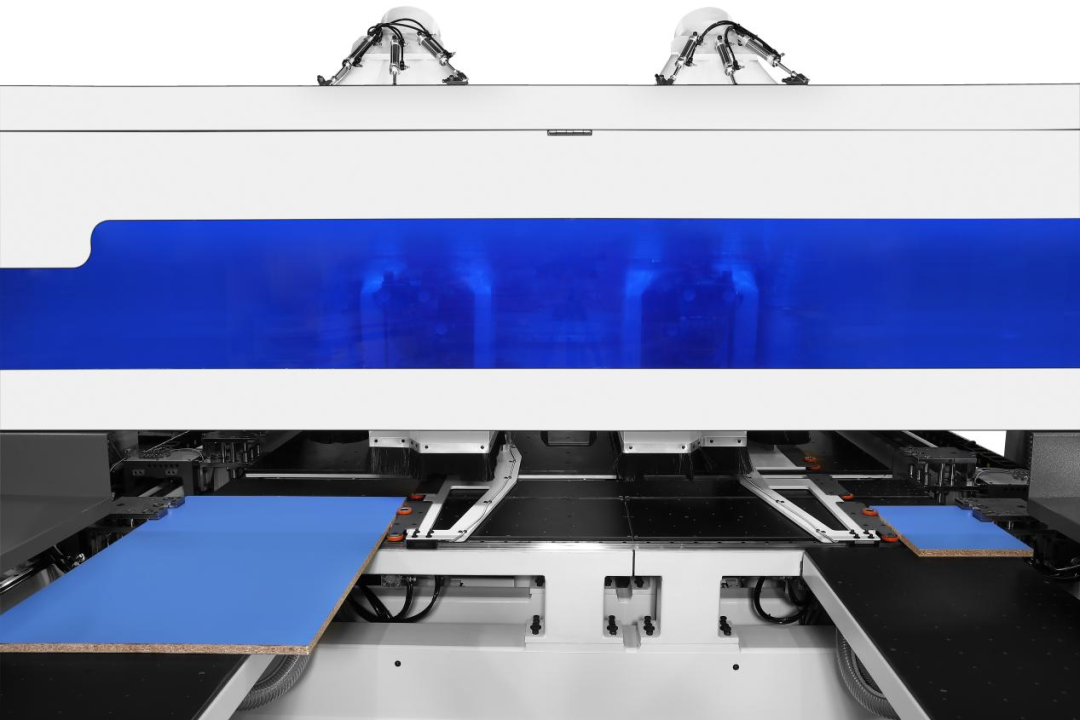
标准工时可以理解为钻孔的实际加工时间,它主要取决于钻孔设备本身的性能,一些中小型定制企业仍在选择使用排钻,因为其效率高、精度好,适合批量大板件的加工,但仍属于半自动化设备,调机和装卸刀具时间长,不适合个性化多品种产品的加工。
相比较而言,数控钻孔设备的自动化和智能化程度更好,产能和效率更高,尤其适合现在的大规模定制。因此钻孔设备本身的性能会带来加工质量和效率的提升,此外,设备的有机组合,产线的互联,信息化的赋能也可以将单个设备的效能最大化。
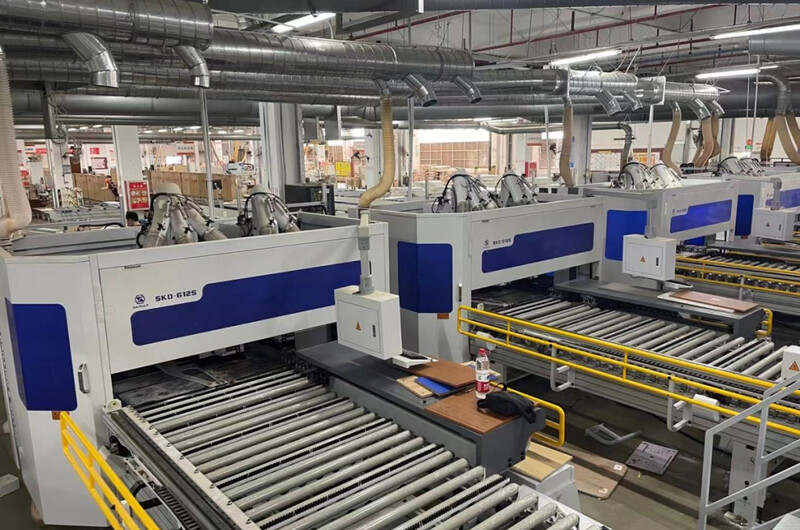
辅助工时主要包含生产准备时间、调机时间、换刀时间、定位时间、首件确认时间、上下料时间等,其中的调机时间与定位时间往往易错且耗时。
对于普通排钻来说,减少定位时间与次数,可以依靠改善作业方法、改善工夹具、提高作业人员的作业转换速度等方法来实现。数控钻孔设备效率高的原因,从某种程度来说,是它较大程度降低了人为操作的比例,依靠设备自身的智能优化。
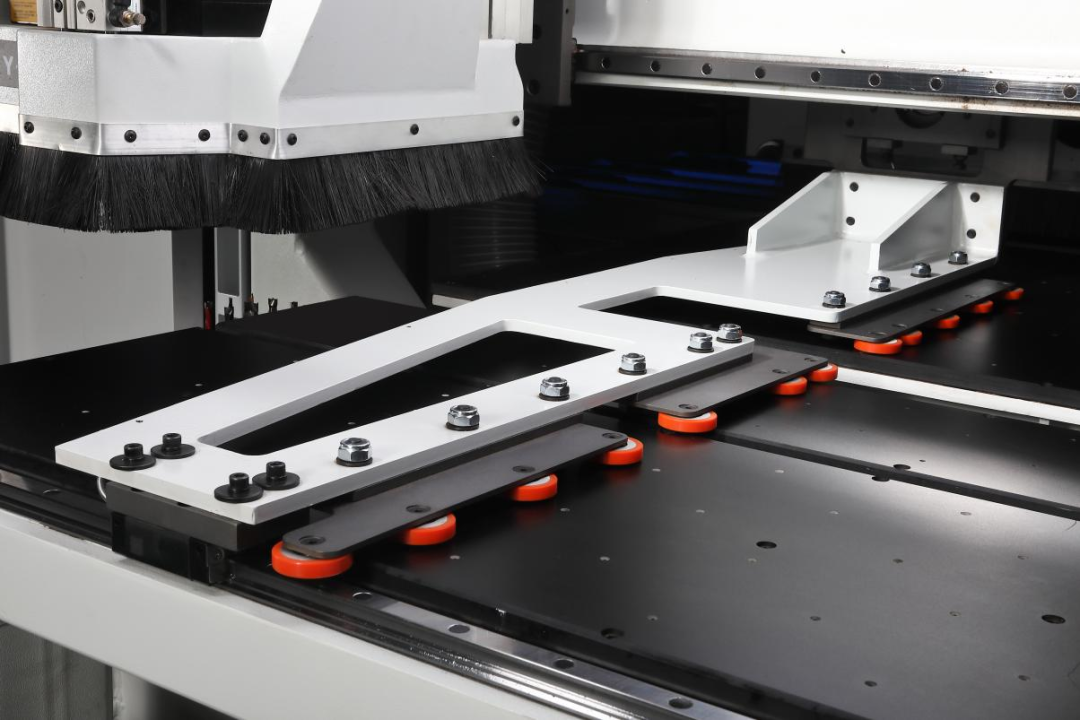
03-4 设备本身的性能
所谓“工欲善其事,必先利其器”,钻孔的质量和效率自然离不开设备本身的性能,不同设备在加工稳定性、加工精度、加工速度方面存在差异,更在自动化、智能化水平上相差甚远。即使是同一款钻孔设备,由于品质和配置的不同,也会带来不同的加工效果。
04 写在最后
当前定制家具生产中的钻孔作业,对钻孔工艺以及设备有比较高的要求,通过改善作业方法、改善工夹具、提高作业人员的作业转换速度等方法降低辅助工时;通过向数控化、自动化、能化设备车间发展提高自身产能,多台设备联合使用优化设备的利用效率,衔接连贯生产线来降低标准工时,从而达到打孔工序的质量与效率的统一
信息来源:鲁班园